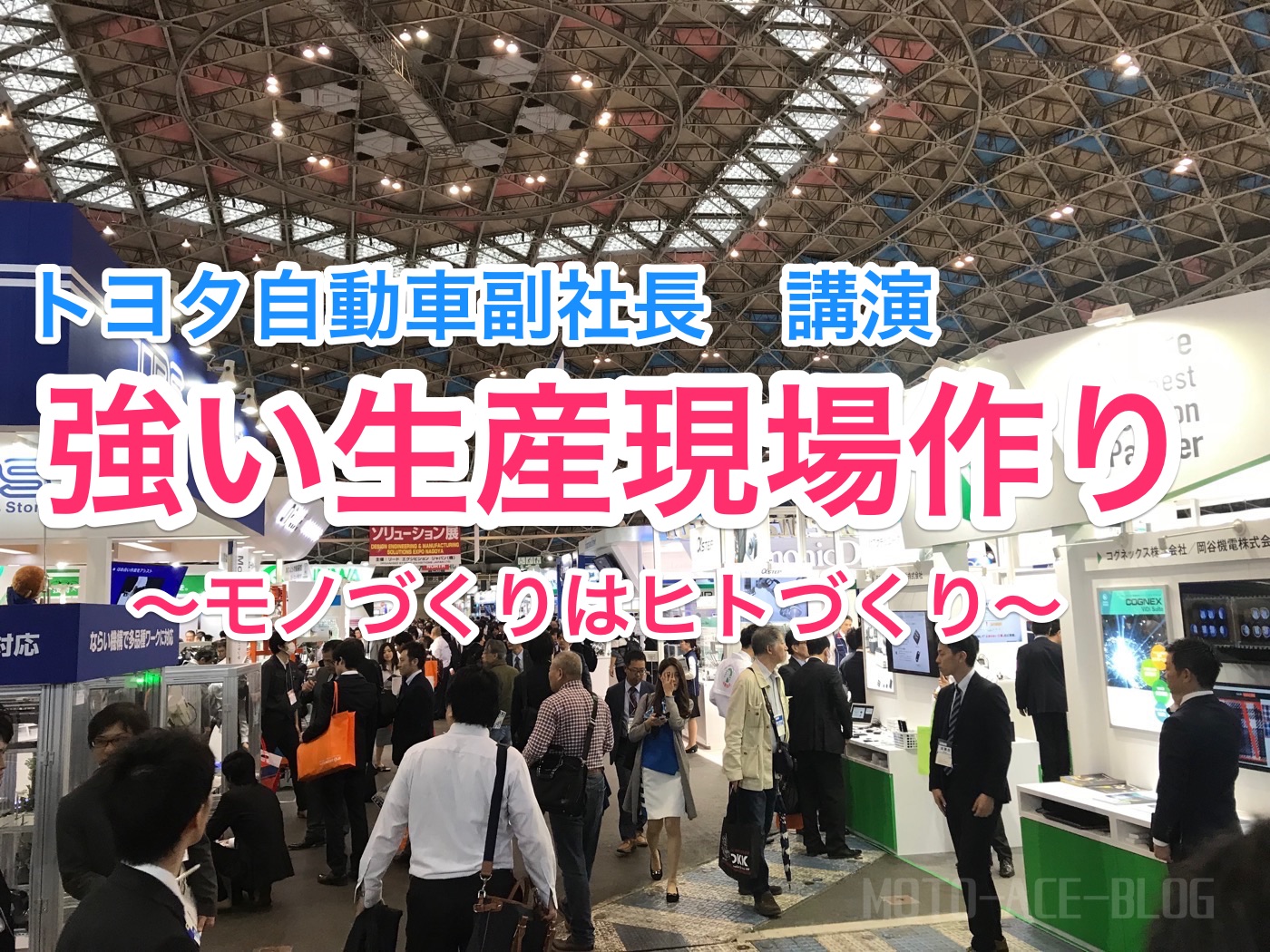
こんにちは!MOTO-ACE-BLOGERの@Andyです。
毎年4月にポートメッセ名古屋で開催される産業技術、産業機械の展示会に情報収集の為に行っています。
その中の客寄せの為に開催される各方面の分野のエキスパートや権威の方の講演会が自分の中では楽しみの一つなんです。
一昨年はホンダエンジニアリングのホットプレス技術開発についての講演を聞き、とても面白い内容でした。
そして今回はトヨタ自動車現役副社長の話を聞けるとの事でまたとないチャンス!! と思い申し込む事にしました。
当ブログ記事はコピー禁止です。詳細→当ブログの記事コピーに関するルール
記事の目次
1. 申し込み料が5000円→11000円と倍以上の値上げ!!
マジかよ!! そんな値上げすんの!! ( ・∇・) と思わず叫びそうになりました。(いや、ちょっと叫んだww)
今までは1講演で約5,000円だったのに倍以上ですよ!! 一瞬躊躇しましたが、今回の機会を逃したら聞けるチャンスはないな〜と思い重い重いクリックボタンを押しました。(手が震えてダブルクリックしまくりw)
Toyota-seminer
2. 公演会場に40分前に到着もまさかの満席!!
どの講演プログラムも結構人気があり、いつも立ち見が出るほどです。 今回は前の方で聞きたかったしパワポの資料が後ろの方の席は画面が小さすぎて見えません。
なので前を狙うべくいつもより10分早い40分前に会場に到着!!
満席!!
なんでやねん!!(°▽°)
第二会場へと行くしかありませんでした。 第二会場はパワポの資料を超大画面で写してくれていたので、視覚的には問題ありませんが、当の副社長本人が見えないのでなんとも寂しい。。。
やっぱり愛知はトヨタのお膝元だけあってトヨタ系の講演は人気があるみたい。
↑第二会場も満席!! 35分前でもこの人の入り。 ヤバし・・・。
3. トヨタ自動車副社長講演|モノづくりは人づくり
約1時間ちょっとの講演でしたが、Andyが覚えている範囲ですが、どんな内容だったかをお伝えします。
以下、コピー及び転載は全て禁止です。コピーした場合は自動的に貴IPアドレスが通知されます。
引用したい場合は当記事のURLを記載頂き、”引用”である旨を明記して頂ければOKです。
当記事のURL等をご紹介頂ければ嬉しいです。
1. 登壇者 河合 満 副社長の経歴
- 1963年にトヨタ養成所に入社(現在のトヨタ学園)
- 入社以来、鍛造(プレス)畑一筋
- 1999年に鍛造部部長
- 趣味は釣り、ゴルフ、庭の剪定、お酒を飲む事。
- 座右の銘:信頼と情熱(時に愛とロマンと言い換えることも)
- 朝と夕方に会社で風呂に入り湯船に浸かる。→鍛造は汗と油に塗れるので必ず風呂に入るそう。
副社長となった今も現場を最も大切にしている。 豊田彰男社長に無理をお願いして自分のデスクを油の匂いのする工場内へ置かせてもらっているそうです。
なんでも、工場から発する音、匂い、煙、機械の音、そういったモノを五感で感じる事ができ、工場の空気が読める。事務所にこもってしまうと、空気の読めない人間になりそうで嫌だ。 だから現場にこだわるし、現場を感じる為にデスクは工場内に置く。 その方が仕事も捗る!! んだそうです。
2. トヨタ自動車のあゆみ
1937年に設立。
現在は「クリーンで安全な商品の提供を通じて、豊かな社会づくりに貢献し、国際社会から信頼される良き企業市民をめざしています。」と時代に合った内容に変化を遂げています。
入社した当初はまさか自分が働いている会社が世界一の自動車メーカーなるとは夢にも思っていなかったそうです。
でも、日本一にはなってみたいな〜! なんて仲間と軽く話す程度だったとか。
3. トヨタを取り巻く環境変化と技術革新
今までだいたい10年に1度のペースで自体を揺るがす大きな出来事がある。
1970年代
オイルショックが発生。 国内は大不況に陥る。
排ガス規制が格段に厳しさを増し技術力の向上が待った無しとなった。 トヨタの技術力で困難を突破。
1980年代
アメリカとの通商摩擦が発生。 トヨタはもちろん日本製のクルマがコテンパンにやッつけられてしまう。 現地生産が一気に加速。 技術を世界に伝承する技術も磨かれ始める。
1990年代
バブルが崩壊。 またも大不況の時代が訪れる。
2000年
ITバブルが弾けてまたも不況に。 追い打ちをかけるように2008年にはリーマンショックにより世界同時不況が発生。
2008年には経常利益2兆円を突破していたが、2009年には一気に赤字へと転落。
2010年
品質問題が勃発。 彰男社長がアメリカ下院議会の公聴会へ出席する。
タイで大規模な洪水が発生、工場が全滅。
東日本大震災が発生。
九州で大震災が発生。
2020年
さぁ何に怒る??
さぁ何が起こる!?
"何も起こらない事が無い" 事は歴史が証明している。
トヨタは今までどんな困難も乗り越えてきた。 それは優れた人材の集団であるからだと自負している。 もちろん優秀な人材を採用するがそれだけでは困難突破は不可能。 技術者として、トヨタ社員としての人づくりを続けてきた賜物。 だからトヨタにはこれから起こる困難を乗り越える自信と確信を持っている。
こうして見ると、どれも大きな混乱ばかりだな〜と感じます。 やっぱり偶然ではなく必然で乗り越えてきたのは間違い無いんだなと確信しました。 トヨタの持つ実力で乗り越えてきたんだと感じます。
4. リコール問題
「2009年2月24日をトヨタ再出発の日」と定めているそうです。 品質は会社の生命線であるとの認識をもう一度改め思い返し、原点である”自動車を通じて豊かな社会づくりに貢献する”為に自分は(トヨタ社員)なにをすべきなのか? をもう一度考えるそうです。
毎年2月24日は品質にかんするミーティングを実施し、この事を忘れず教訓としている。
リーマンショック、リコール問題など一気に荒波に呑まれたがV字回復を成し遂げた。その理由は何なのか? と多くの方から問われる。 が答えはいつも変わらない。
これから起こる大きな問題も、必ず乗り越えられる。 なぜなら、過去全ての困難を当たり前の事を当たり前に実行し行動して解決してきた歴史が証明してきた。
1.内外の法およびその精神を遵守し、オープンでフェアな企業活動を通じて、国際社会から信頼される企業市民をめざす
2. 各国、各地域の文化・慣習を尊重し、地域に根ざした企業活動を通じて、経済・社会の発展に貢献する
3. クリーンで安全な商品の提供を使命とし、あらゆる企業活動を通じて、住みよい地球と豊かな社会づくりに取り組む
4. 様々な分野での最先端技術の研究と開発に努め、世界中のお客様のご要望にお応えする魅力あふれる商品・サービスを提供する
5. 労使相互信頼・責任を基本に、個人の創造力とチームワークの強みを最大限に高める企業風土をつくる
6. グローバルで革新的な経営により、社会との調和ある成長をめざす
7. 開かれた取引関係を基本に、互いに研究と創造に努め、長期安定的な成長と共存共栄を実現する
仕事をする上で常に上位にこの企業理念の考え方が位置していて、迷った時や判断に困った時にもう一度立ち返る、戻る場所。 当たり前の内容になっているが、この当たり前を続ける事が難しい事をトヨタは全社員が共有できている。 ここもトヨタの強みであると言っていました。
ここは自分も大いに納得しました。 たとえば子供の頃は元気に大きな声で「おはようございます!」と、挨拶しましょうね!
って誰しも習った当たり前の事なのに・・、大人になると・・? 挨拶できない人の方が多くなってしまう。。。
そもそも”当たり前”ってトヨタからすると逃げの言葉なのかも。 当たり前が無い事を前提とすると物事が違って見えるのかも? そんな事を想いながら聞いていました。
4. 手作業の大切さ|~自動化とは~
手作業ラインこそ技能の原点と考えている。 必要な物を、必要な時に、必要なだけ、つくる。→実際に実行するには技術が必要。 その技術は改善から生まれる。
トヨタでは”7つのムダ”と言う考え方を持ち、徹底的にいつも見直している。
- 加工そのものがムダではないか?→行程・工数の見直しできる。
- 作り過ぎのムダはないか?→物は売れる速さで流れる。
- 在庫のムダはないか?→スペースと管理工数が増える。
- 手持ちのムダはないか?→作業待ちの状態の事。付加価値を生まない時間。
- 動作のムダはないか?→しゃがむ、手を伸ばすなどムダな動きを無くす。
- 不良のムダはないか?→手直し、検査、作り直しなど無駄を生む原点となる
- 運搬のムダはないか?→仮置き、積み直しなど本当に必要か?考える。
1.加工のムダ
従来からのやり方の継続といって、本当に必要かどうか検討せず、本来必要の無い工程や作業を行うこと。
2.作り過ぎのムダ
その時点で必要のないものを余分につくること。 ものは売れるスピードで流れながら形を変える。売れるスピード以上に速度を上げるには余計な燃料が必要になりコスト増につながる。
3.在庫のムダ
完成品、部品、材料が倉庫など保管され、すぐに使用されていないこと。 運搬、管理、保管に新たなコストが掛かって手間とコストの増加につながる。 明確な目的のない在庫は全てムダである。
4.手持ちのムダ
作業者が何もせず、待っている状態を指す。 前工程からの部品や材料を待って仕事ができない状態(待っているだけ)は何も付加価値を生まない。 作業者が待たないように作業スピードを調整してしまうので、ムダを最も発見しにくいからこそ、発見するテクニックが必要とされる。
*見落とすとカイゼンに繋がらない。
5.動作のムダ
探す、しゃがむ、持ち替える、調べるなど作業者の不必要な動きのこと。 最小限の動きで完結できることを目指す。
6.不良のムダ
不良品を廃棄、手直し、作り直しすること。
不良品は常に0を目指す。 発見が遅れるほど、トラブルが大きくなりそれに伴うムダも雪だるま式に膨れ上がる。
この考え方は全く知りませんでした。 トヨタのカンバン方式は業界では超有名だし、本でも勉強していたので知っていました。
しかし”7つのムダ”と言う考え方を提唱し、習慣づけている事は知りませんでした。
新たな発見!!
そしてこの「ムダを無くす為のカイゼン」こそ技能を高める最高の舞台と捉えているそうです。
技術と技能、技能の技術はともにスパイラルアップするしか方法が無い。 人間の技能が上がらなければ技術も上がらない。 技術を高めるには技能を高める。 これを徹底する最高のチャンスがムダの中にある。 だからムダのカイゼンは技能を高める事であるから、トヨタでは徹底して活動している。
普通、作業者任せにしてしまうけど、会社の資産にする為にチームを作ってカイゼンし、記録と記憶に残し技能を蓄積するってことか・・!
恐るべしトヨタの行動力。。
トヨタが生まれ変わる前は、自動化を”人のやれない事”の考え方を基に強力に推進してきた。
すると機械は複雑、価格が高い、加工が見えない、保険が必要な機械が沢山出来上がった。
複雑な機械は故障した時、原因究明に時間がかかる。 また故障個所にアクセスする手間も掛かる。結果機械の組み立てコスト、修理コストも高くなり良い事は何一つない。 →機械はシンプルであるべき。
その機種専用の機械を0から設計製作するのでコストが高い機械になる。 しかも専用設計されており改造できなかったり、ワークの小変更に直ぐ対応できない。 → フレキシブルな機械であるべき。
専用に設計するので、安全を最優先すると加工場所が奥になり加工そのものが見えない。→トラブルの過程や結果、が見えないので時間が掛かる。 また実績のない機械は安全を優先するがあまり、見えなくなる部分が多くなる。 → スリムな機械であるべき。
複雑で見えない機械が壊れると復旧に時間がかかる事から、在庫が必要になる。 機械の予備品も多めに持っておきたくなる。夜勤の保全作業者も多く確保する必要が出るなど、ムダの温床になる。
その結果リーマンショックが発生し生産台数が激減した時、一つの物しか作れない機械だらけの工場は全く可動させる事ができなかった。
この「最高にムダになった工場現場=最高に学べる現場」と捉え、またとない最も技能を高める舞台を利用しトヨタは勉強し技能を高めてきた。そして学んだ結果、
の考え方を基に機械化と自動化を進めている。 大量生産&大量消費の時代には前の考え方が最も適していたが、時代と共に変化が訪れる。 トヨタは変わる事を恐れず、自ら変わる事のできる集団である。 しかしそれは多くの失敗から学んでいる。 ここもトヨタの強みです。 とおっしゃっていました。
トヨタはまるで中小企業並みの行動力があるな・・・。
4. 手作業の大切さ|~日本のものづくりの優位性~
レクサスのレザーシートの縫製作業は現在ハンドメイドで行われている。 レザーのしわを伸ばしながら縫う作業はまだロボットではできない。 ではなぜロボットができないのか? → 人間が数値化できないからロボットに教える事ができない。
同じ作業でも短時間で品質の高い仕事をする人は、必ず「勘とコツ」(トヨタでは”カンコツ”と言う)を持っている。
カンコツを数値化できれば、ロボットへの置き換えが可能になる。
そのカンコツを養う為には手作業が欠かせない。 なぜならロボットからカンコツは生まれないから。
なのでトヨタは現在”手作業”にトコトンこだわっている。 カンコツを習得する事は技能を習得する事と同じ。
習得した技能を数値に置き換え技術を向上させる→スパイラルアップを実現。
ロボットだけがどれだけ高性能になろうが、技能が伴わなければ良いものづくりはできない。
近年、社内技能交流会、からくり大会、技能五輪大会などあらゆる技術交流会を実施したり積極的に参加している。 トロフィーなどは自ら全ててづくり。
自分達でものづくりができる → 使う道具や機械を直せる → 道具や機械を進化させられる
このスパイラルが非常に大切である。 特に部署のメンバーと共にチームを組む事で様々な意見を聞く事ができ、交流も深まるので、トヨタが大切にしている人材育成方法のひとつと聞きました。
また社外イベントの技能五輪大会にも積極的に参加しているそうです。 そして昨年の2017年大会では30種目中、17種目で中国が優勝したそうで、今後中国の技術力は間違いなく伸びる。しかも凄い成長スピードで発展する! と語気強めに仰っていました。
インターネットのお陰で情報伝達に革命が起きた恩恵で、ものづくりもノウハウが一瞬で伝わる時代が来ていると言う事なんでしょうね。 かつての日本がそうだったように、中国が安くていいクルマを作れる時代はすぐそこって事に、気付いている人少しづつ増えてきたんだと感じました。
5. 手作業の大切さ|~手作業から得た改善事例~
事例1. クランクシャフト鍛造行程
クランクシャフト製造コストの内、70%が材料費で占められる。→ 材料費を下げるには捨てる材料を少なくする事が効果的である。
プレス工程を手作業で行い、改善できるポイントを徹底的に洗い出した → 結果、元は1行程だったが、1行程増やして2行程とする事で端材の量を削減に成功し、大幅なコストダウンに繋がった。
手作業でプレス工程を行う事で、カンコツを形成→数値化→行程不足があぶりだした。
事例2. ボデー溶接ライン
通常はほとんど無人でスポットなど溶接工程が進んでいく。 → あえてラインを停止させ人の手で溶接作業する時間を設ける。
手作業をもっと速く安定させるには?の観点で方法を工夫する → 人間が上達する(カンコツを掴む) → 数値化する → ロボットへティーチングする。
ラインが止まる時間はもちろん生産できないが、トータルでみればカンコツを習得する時間があるお陰で品質の高いものづくりができる技能が身につき、トラブル対処も速い。 ライン停止していない時より生産数は向上した。
事例3. ロボットに「技」と言う文字を毛筆で書かせる
書道プロはもちろん、上手く書く事ができる。 しかし機械に同じことをやらせると全く上手く書けない。 毛筆には跳ね、止め、払い、返し、など様々なテクニックがあり、それぞれ向きやスピード、押し付ける力などが異なる。 手首の細かな動き、腕の動きなど多岐に渡る。
プロはもちろんそれらのカンコツを持っている。 → プロのカンコツを数値化 → ロボットへティーチング → ロボットがプロと同じ字を書けるようになった。
つまり、人間の技能が上達しなければ、ロボットも同じ事はできない。ロボットの実力は現時点人間を超えられない。 カンコツを磨き機能を高める事がものづくりの原点である事に、今後も変わりはない。
6. 人材育成の重要性|~良き人間関係~
2014年9月、全国を揺るがすニュースとなった御嶽山の噴火。 残念ながらトヨタの社員の方が命を落としてしまった。
部下を想う会社トップの彰男社長は亡くなった方のデスクに訪れ、献花と黙祷を捧げたそうです。(講演会場ではその時の様子を撮影した写真を見せて頂きました)
彰男社長は、部下や社員の事を常に想っている。 その事は社員にも浸透している。
世間ではパワハラ、モラハラ、最近の若いもんは、などと言う単語は珍しくなくなりました。 トヨタでは上司と部下がコミュニケーションを取る時には、「心」を通す事が必要不可欠と考えているそうです。
どんな時も「心」をすっとばしてはなりません。 例えば係長が課長を飛ばしていきなり部長に報告。 若しくは専務が部長、課長をすっ飛ばして係長に指示を出したらどうなるか?
もちろんTPOによって順序を飛ばす事はあっても、「心」を飛ばす事は許されない。 心を通じてコミュニケーションを取る事を大切にしている。
そうでなければお互いに信頼関係を築く事ができず、組織としての力を発揮させる事ができなくなってしまう。
特に厳しい言葉の裏には、愛情が不可欠。 相手を想うからこそ厳しくなるのであって、気に入らないから怒るのではない。 ここをはき違える上司が日本は多いのではないか?
7. 人材育成の重要性|~人を動かす気配りと心の反応~
自らくばれ!
上司たるもの、目配り、気配り、心配り、を常に行う。 自分が部下に配るのである。 そして配った後の反応を見逃してはならない。 つまり鈍感では上司は務まらない。 必ず敏感である事が上司の条件である。 上司は部下を選べるが、部下は上司を選べない事を肝に銘じるべき。
敏感であれ!
想いを共有する事がとても大事。 それは仕事に限らずプライベートな事、趣味や家族の事、辛い事など含めてどれだけ想いを共有できるかを、信頼関係を築く上で大切にしてきた。
部下を導く為には、心を通し、想いを敏感に感じ取り共有できるかがポイント。
現地・現物!
部下と共に、現場で現物を確認する事が大切。 におい、音、空気、様々な情報を総合的に判断するには現場・現物以外にあり得ない。 現場・現物で判断しない上司は信頼されないし、部下の洞察力を甘く見てはいけない。
打席に立たせる!
バット、ヘルメットを手に入れた部下にはドンドン打席に立たせる。 打てる打てないじゃなく「打つために何をするか?」を考えさせる最高の勉強をできる場所。 ヘルメットの場所、ヘルメットの機能、ヘルメットの使い方を教えるのは上司の使命。
ヘルメットを被らず打席に立ってしまったら全て上司の責任。 ヘルメットの大切さを理解させられない上司であると言う事。 打者は何も悪くない。
若者は髪型が崩れるからヘルメットを被りたくない。 → でも「ヘルメットを被らないと上司に迷惑が掛かってしまうから、上司の為に被ろう」と思わせる教育を!
8. 人材育成の重要性|~100年に一度の大変革時代~
インターネット技術が発展し、IOT、AI、VRなど様々な異種分野との融合が起こる時代に入っている。電気とインターネットは相性が良い。 エンジンをインターネットで直接制御する事は難しいが、電気モーターなら直接制御する事ができる。
トヨタのハイブリッドモーターは、トヨタの現場の人間を集めて作り出した。 電気屋を集めてモーターを作っているのではない。
燃料電池のFCスタックと言う部品は、溶接工がつくった。 トヨタのものづくりは人づくりであるから、人を育てる事から新技術がはじまる。 今後も不変である。
今は全てにおけるスピードが速くなったので簡単に乗り遅れる。 勝つか? 負けるか?の時代はもう終わった。 今は生きるか? 死ぬか? の時代。
作るものは変わるが、ヒトがモノを作る事は変わらない。
会社の成長は、ヒトの成長。 会社を育てる事は、ヒトを育てる事。
以上、ご清聴ありがとうございました。 と河合副社長の締めのご挨拶で講演が終わりました。
4. 副社長 河合 満さんの講演を聞いて
今回でトヨタの講演を聞くのは3回目になりました。
毎回思うのが、トヨタ程の巨大企業なのに話を聞くといつも小さな企業に感じます。もちろんいい意味での小さな企業なんですが、動きが早いし心が温まると言うか、そんな感じになります。
トヨタとして柔軟に考え方と行動を変える部分と、絶対に変えずに伝統を守る部分といつもはっきり分かれているな~と思います。 何と言えばいいのか分かりませんが、芯の部分はどんな困難でもブレる事無く、見に付ける枝葉を柔軟に変えていると思います。
それから、上司は、こころ、を通して、部下に接する。 これも当たり前のようで、つい忘れてしまう事だなと思います。 やっぱり部下や後輩は、上司&先輩に対して意見しにくい立場です。
その事を上司が本当に理解しているか? こころをすっ飛ばしてコミニュケーションを図っていないか?
自分も常に!強く!意識して即実践! したいと思います。
ものづくりは、ひとづくり。 トヨタ式の考え方の意味をシェアできれば嬉しいです。
会場内は撮影&録音等ができず、メモを走らせまくっていた。
上手くまとめられず、読みにくい文になってしまいすみません。
最後までお読み頂き誠にありがとうございました!!
Andy